Sheet Metal Fabrication: From Concept to Finished Product
- Brett Brumm
- Dec 10, 2024
- 4 min read
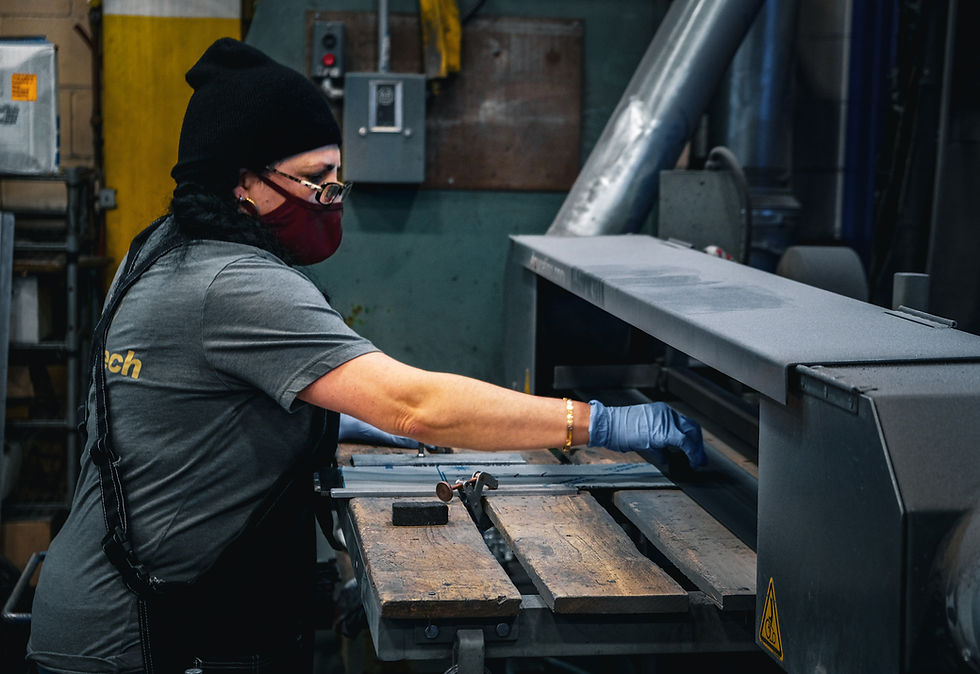
Sheet metal fabrication is the backbone of many industries, from construction to automotive, and understanding the intricate process that turns an idea into a tangible sheet metal product is fascinating. In this comprehensive post, we explore the stages of sheet metal fabrication, the remarkable technologies driving it, and how it delivers solutions across diverse sectors.
In partnership with Advantech Industries, a leading provider of sheet metal fabrication solutions, we're peeling back the layers of this complex metalworking process to showcase the transformation of raw materials into finished goods. Whether you're an industry professional seeking insights or a curious mind looking to understand how your car's frame or your home's HVAC system came to be, you'll find this deep dive invigorating and informative.
Transforming Metal for the Modern World
Metal fabrication is a silent hero in modern construction and innovation, required for everything from tiny components in electronics to vast panels in skyscrapers. Sheet metal fabrication, in particular, is a precise and demanding field that takes raw metal sheets and transforms them into specific shapes and forms. This detailed process provides the foundation for so many of the products we rely on daily.
Advantech Industries excels in this arena, known for its commitment to precision, quality, and excellence. Their capabilities span a wide range, from cutting and bending to welding and finishing, enabling them to produce solutions for industries that have stringent requirements for precision and durability.
Understanding the Process
The sheet metal fabrication process is an orchestrated dance of machinery, materials, and expertise. Each step demands attention to detail and an understanding of the material's characteristics. Here's a breakdown of the typical stages:
Design and Prototyping
The process begins with an idea. A client may approach Advantech Industries with a concept for a component or product. Using advanced CAD software, the design team translates this concept into a digital model, considering factors like function, form, and fit within the larger product or structure.
This phase often leads to the creation of a prototype. Prototyping is a crucial step to test the design's viability, make adjustments, and ensure that the final product will meet the customer's specifications.
Material Selection
Material selection is a pivotal decision that can influence the project's success. Factors such as the metal's strength, corrosion resistance, and formability must align with the project's requirements. Common materials include stainless steel, aluminum, and carbon steel, but the possibilities extend into a variety of alloys tailored to different needs.
Advantech Industries’ material expertise is crucial here; they advise on the best materials for the job, taking all the variables into account.
Cutting and Shearing
Once a design is set and materials are in hand, the actual fabrication can begin. The cutting and shearing stage involves a variety of techniques from traditional guillotine shears to high-tech laser cutting machines that are capable of cutting intricate designs with micron precision.
These cutting methods define the initial shape of the metal sheet, setting the stage for the subsequent forming and assembly steps.
Forming
Forming shapes the cut pieces into their desired forms using techniques such as bending, rolling, and stamping. This stage requires expertise in tooling and machinery to ensure that the metal retains its integrity and that each piece is formed exactly to the design's specifications.
Companies like Advantech Industries invest heavily in machinery that offers repeatable precision, from small components to large scale pieces.
Assembly and Joining
Once the components are cut and formed, they are assembled using methods such as welding, riveting, and even adhesive bonding. The goal is to create a unified structure that is as strong as it is seamless.
Welding, in particular, is an art that requires skill and finesse. Advantech's certified welders ensure that every weld is of the highest quality, providing stability and performance over the product's lifetime.
Finishing
The finishing step adds the final touches that protect the metal and enhance its appearance. It includes processes like painting, powder coating, polishing, and plating.
Finishing not only makes the product more aesthetically pleasing but also adds crucial attributes like weather resistance, dielectric strength, and even antimicrobial properties.
Inspection and Quality Control
Before anything leaves the fabrication floor, it undergoes rigorous inspection. Each component is measured against the design's specs, tested under relevant conditions, and examined for any flaws.
Advantech Industries’ dedication to quality control ensures that every product is ready to perform to the highest standards once it reaches the client.
Delivery and Support
The final step is getting the product into the client's hands. Whether that's shipping components to be integrated elsewhere or delivering a standalone product, a thoughtful delivery process ensures that the product arrives in the same condition it left the factory.
Advantech Industries also offers support services to ensure that clients have everything they need to make the most of the sheet metal solutions, from documentation to field support.
Sheet metal fabrication is both an art and a science, with each stage demanding a unique set of skills and tools. The industry's future is an exciting blend of tradition and innovation, with new technologies and materials continually expanding what's possible.
Advantech Industries' commitment to quality and expertise positions them as a leader in the sheet metal fabrication world. Their dedication to the craft and their willingness to push boundaries make them a reliable partner for anyone with a sheet metal need.
Whether you're an industry professional or a curious consumer, the world of sheet metal fabrication is one filled with challenges, opportunities, and endless ingenuity.